证券代码 830978
从毛坯铸造到精密加工,高精度三维视觉贯穿铸造生产链路各3D测量环节
2024.07.03
在工业制造中,很多的零部件的生产会集成多道生产工序,例如汽车缸体、螺杆风机核心部件——转子等产品的生产过程中,会先行铸造毛坯,再进行机加工生产。
高精度三维扫描技术作为一项准确、高效、便携的通用型3D测量工具,能够在各工序间都发挥应用。本期,我们就走进铸造这一生产链路,来了解高精度三维扫描在“从毛坯铸造到精密加工”的整个生产链路中发挥的作用,以先进测量方式赋能,推进产品尺寸质量的提升和生产过程的提速。
01 模具生产环节
非接触光学测量,高效完成复杂形状模具形位公差检测
在铸造成型中,模具是铸件成型的直接工具,其尺寸和形状质量,直接决定了最终铸件的形状与尺寸精度,对模具进行严格的尺寸检测是铸造过程质量控制的关键环节。
但是,铸造模具以及型芯一般形状复杂,给尺寸和形状的测量工作,带来了一系列的挑战。传统的模具检测手段主要依赖人工测量和接触式检测技术,这些方法不仅效率低,而且对模具的不规则曲面及内部复杂结构覆盖不足。
相比之下,高精度三维扫描技术凭借其非接触式测量的优势,不受模具形状限制,能够快速、准确完成复杂形状模具的形位公差检测,显著提升了模具检测的精度与效率,缩短模具的生产周期。
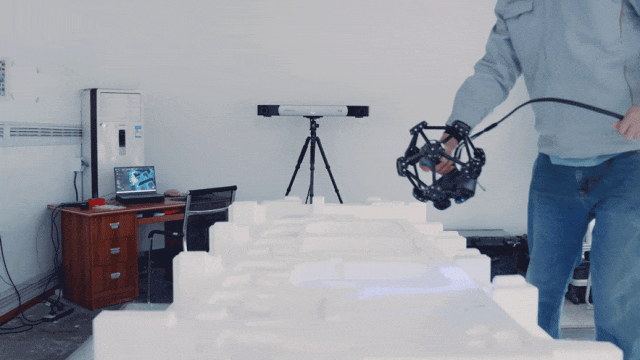
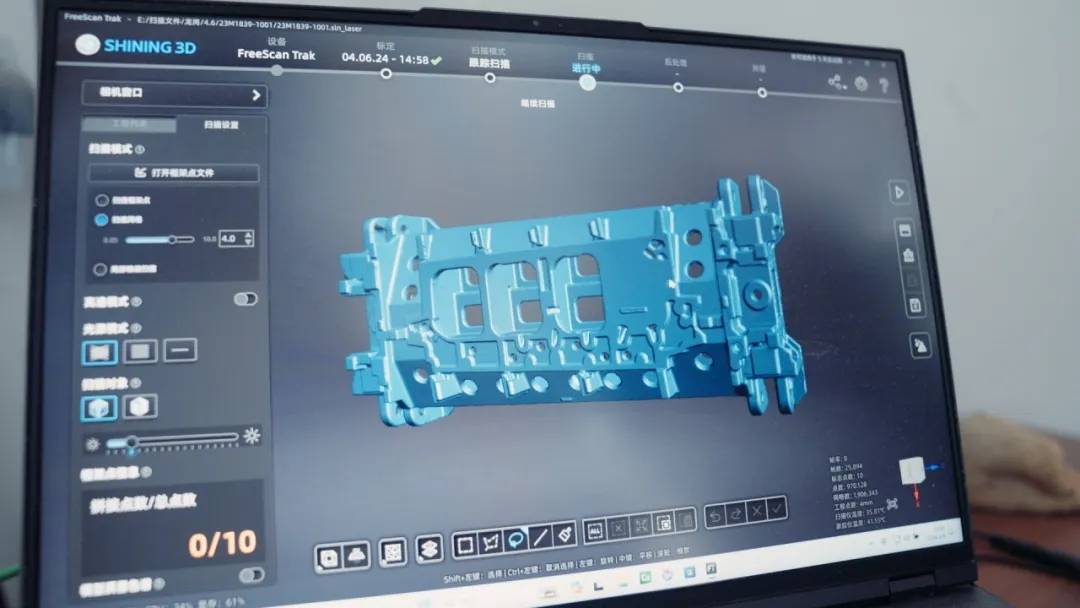
消失模(型芯)检测:
FreeScan Trak Pro2 对4米长的消失模进行三维扫描,仅需10分钟左右便可获取三维扫描数据,完整检测流程在半小时内,传统检测方式1-2小时。
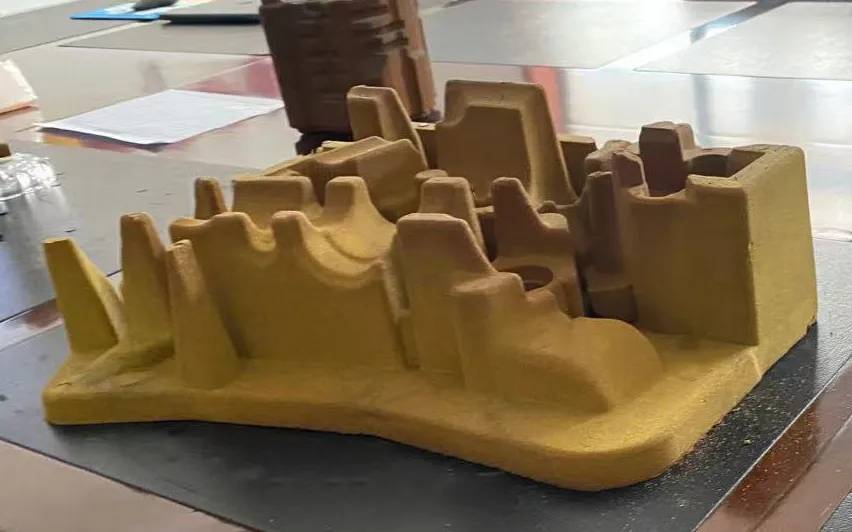
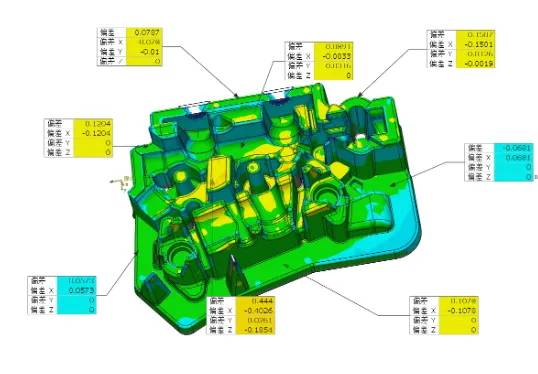
砂型模具检测:
使用FreeScan UE直接三维扫描砂型模具,50*30*20cm的大小范围,3分钟即可获取完整的三维数据,将三维扫描的数据导入检测软件,2分钟即可完成整个模具的全尺寸测量。
02 铸件尺寸检测环节
一次扫描即可完成全尺寸检测,测量效率大跨度提升
成品尺寸检测是铸造质量控制的重要一环,铸件是否变形,后续装配位置的尺寸、位置关系是否准确,都至关重要。在传统测量方式中,基本靠人工进行点、线的测量,且基本上都是单尺寸测量,即一个尺寸信息就需要测量一次,若测量100个尺寸,则需要测量100次,效率难以实现突破性提升。
而高精度三维扫描仪可以实现全尺寸测量,将三维扫描仪获取的数据导入检测软件,与原始设计图纸对比,即可一次性量化所有形位公差不符合生产要求的部分,生成直观、翔实的检测报告。一次扫描即可完成全尺寸检测,测量效率大跨度提升。
此外,高精度工业三维扫描仪环境适应性强,使用灵活,在产线上即可完成三维检测,无需像三坐标一样搬运至专用测量室,进一步节省测量时间。
一次扫描,即可完成铸件的全尺寸检测
03 精密加工环节
便携式方式实现加工余量可视化,实现高质高效生产
针对精密零部件的制造,铸件往往作为初成型的毛坯存在,通常需要通过精密加工等手段,对铸件进行精细化加工。
这类经过深加工的铸件,其尺寸精度直接影响到与其他组件的装配吻合度以及整个系统的运作效能。在加工过程中,高效准确地把握加工余量,则是提升效能的关键所在。
高精度三维扫描凭借其高精度、高效率和高便携性的优势,能够直接在机床上完成加工对象加工余量的测量。这种高效可行的方式,为精密加工提供了可视化条件,能够精准控制进刀量,既保证产品精度,又保障生产效率。
解决了传统方式下,反复使用三坐标测量而导致的效率低下难题并杜绝了过切报废,保障良品率,实现了生产效率和产品良率的双重提升。
从模具生产-铸件检测-精密加工,高精度三维扫描技术贯穿了铸造生产链路各3D测量环节,并实实在在帮助各环节实现了效能的提升。接下来,先临天远高精度3D视觉技术将持续赋能铸造行业的优化升级,为铸造产业注入强劲的数字活力!